The evolution of inventory management: From manual spreadsheets to modern automation
Managing inventory in support of the government? Then you can't afford to leave anything to chance - and you definitely don't want to do it manually.
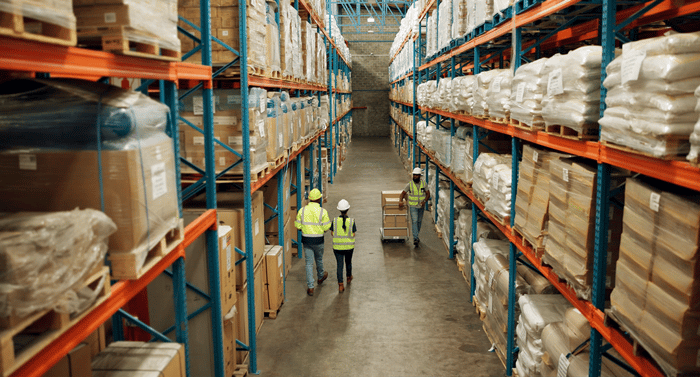
Picture this: your business has just won a massive contract to procure or manufacture items for the government, but your warehouse is in a state of disarray.
For years you’ve managed your assets and inventory through spreadsheets and manual effort, resulting in an inventory management system that is more ad hoc and eyeballed than it is refined and organized.
In this blog series, we’ll explore why businesses that procure and manufacture items for the government need to invest in an automated inventory management system and how you can increase your ability to meet contract requirements when it’s integrated with an ERP.
Spreadsheets aren’t enough
Regardless of the business you’re in, using spreadsheets for inventory management brings on significant challenges such as:
- The potential for human error: Manual data entry into spreadsheets is susceptible to mistakes, leading to discrepancies that can affect inventory accuracy. And businesses using paper to keep track run the risk of losing important information when records aren’t well organized.
- Too time-consuming: Updating and maintaining spreadsheets is a tedious process that can detract from other essential inventory management tasks.
- Limited scalability: As businesses grew, the limitations of spreadsheets became evident. Managing large volumes of inventory data manually was not sustainable.
- Lack of real-time data: Spreadsheets do not provide real-time updates, leading to potential delays in decision-making and accurate inventory tracking.
Why should a GovCon care?
GovCons should care about switching to automation because the alternative leads to mistakes. When inventory numbers are wrong, it can lead to shortages or overstocks, reducing profit.
The need to track Government Furnished Material (GFM) is a mandatory requirement. If you have been given material, you don’t own it – the government does. You need to know where it is located, how it is being used, and ensure accurate inventory tracking for compliance.
When you secure your first Cost Type contract, you’ll quickly realize the necessity of tracking and segregating all the inventory bought for that project. When you don’t own the materials, maintaining an effective inventory management system becomes essential for both government compliance and project success.
While fixed-price contracts may not require the same level of compliance , you’ll still want to know the status of your inventory for the project. Without a clear understanding of inventory costs, you won’t know if your project calculation is correct. Adopting an automated inventory management system ensures you have real-time visibility into your asset and enables you to track costs accurately.
The shift to digital solutions
The majority of successful businesses have made the shift to invest in software to automate and better track many of the previously manual functions. With the creation of cloud-based inventory management software and the ability to scan track physical assets (i.e., RFID, barcode, IoT) businesses can remove spreadsheets and all of its pitfalls from the process. This increases the likelihood of compliance and effective contract completion.
As reported by Unanet customers, the shift to digital solutions for asset, inventory management, and manufacturing can result in:
- Reduction in inventory carrying costs by up to 30%
- Increase in operational efficiencies by 25%
- Reduction in time spend on inventory tracking by up to 40%
Benefits of digital inventory systems
Here are several examples of scenarios where you might see the benefit of a digital inventory system:
With regard to GFM, imagine a situation in which you win a Direct program execution model (DPEM) fixed-price contract to assemble drones for the Air Force. Managing your inventory digitally keeps your organization accountable for all GFM with automated inventory tracking via barcode scanning and audit trail. Using an automated inventory management solution ensures you maintain clear accountability and accurate inventory tracking, crucial for both compliance and profitability.
Contracts that put a heavy reliance on the contractor sourcing its own materials can benefit from using an automated inventory management system. Contractors can track orders from specific vendors, using tools like a vendor scorecard to source materials in a cost efficient and time efficient manner.
Consider a situation involving a cost-plus contract. Say you are working on a research and development (R&D) project that will require you to purchase a large amount of raw materials for prototyping or different types of items to test assembly performance. These materials must be tracked when they are used to produce a product or item. Having the ability to automatically track inventory levels and place orders when needed reduces delays. With barcode scanning that automatically tracks asset type, businesses can better track product versions, allowing them to reproduce effective products or identify defective products.
The modern era: Automated inventory management systems
The evolution from manual inventory management using spreadsheets to modern, automated inventory management systems marks a revolutionary shift in the way many businesses – including GovCons – manage and track their assets.
These digital solutions not only mitigate the risks associated with human error and inefficiencies but also ensure compliance, improve inventory accuracy, enhance inventory control, and streamline operations.
By embracing these innovations, organizations can confidently navigate the complexities of their contracts. They can set themselves up to win further business, completing projects with greater reliability.
Looking to make business easy while freeing up more time to do the work that matters? Learn how Unanet can help. Schedule a demo today.