Ten MMAS requirements government contractors need to know
Learn the key compliance requirements for Material Management and Accounting Systems (MMAS) to keep your government contracts on track.
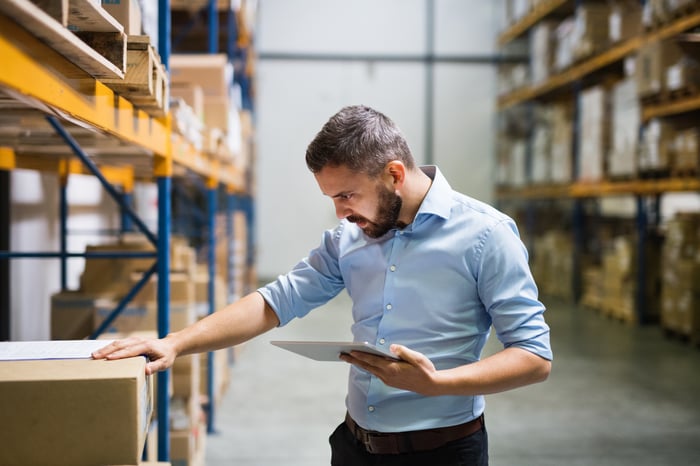
In the world of government contracting, clarity and compliance are critical. This is particularly true when it comes to Material Management and Accounting Systems (MMAS), a keystone on which your business operations must be built.
For government contracting companies (GovCons), the federal government regularly audits for MMAS compliance. Let’s dive into what MMAS is and what specific requirements you’ll need to keep on top of.
What is MMAS?
Before diving into the specific requirements, let’s explore the origins of Material Management and Accounting Systems (MMAS).
First introduced in 1989 through the Defense Federal Acquisition Regulation Supplement (DFARS) MMAS requirements were first introduced in 1989 as part of the Defense Federal Acquisition Regulation Supplement (DFARS). MMAS ensures that you, as a government contractor, follow strict guidelines for managing materials and maintaining an accurate accounting system.
At its core, MMAS compliance ensures you:
- Accurately track the duration and status of contracts.
- Maintain seamless tracking, costing, and accounting for physical items or product manufacturing.
The goal is to prevent material loss or misuse while ensuring all transactions are properly recorded. This provides transparency and accountability to the federal government, ensuring you remain a responsible steward of taxpayer dollars. The Defense Contract Audit Agency (DCAA) conducts audits to verify that your contractor business systems maintain compliance with these standards.
Now that we’ve defined MMAS, let’s explore the ten requirements you need to meet to stay compliant.
At its core, these criteria are designed to make sure contractors:
- Accurately track the age or duration of contracts
- Maintain a seamless flow in tracking, costing, and accounting for physical items or product manufacturing
The goal is to prevent material loss or misuse while ensuring all transactions are properly recorded. This provides transparency and accountability to the federal government, ensuring you remain a responsible steward of taxpayer dollars. The Defense Contract Audit Agency (DCAA) conducts audits to verify that your contractor business systems maintain compliance with these standards.
Now that we’ve defined MMAS, let’s explore the ten requirements you need to meet to stay compliant.
System description: Policy, procedures, and operating instructions
The first MMAS requirement is to have a comprehensive system description. This includes detailed policy documentation, clearly defined procedures, and accessible operating instructions.
You should conduct a self-assessment of your people, processes, and tools to ensure you're ready to provide this information to the government. By identifying and resolving these issues early, you can ensure that your material management and accounting system remain accurate and compliant with government regulations.
Material requirements: Time-phased materials, bill of materials and planning accuracy
Material requirements, including time-phased materials and bill of materials (BOM), should be accurately documented. To meet this MMAS requirement, you need to focus on two key goals: achieving 98% accuracy in your bill of materials and ensuring a 95% accuracy rate in your master production schedule.
System monitoring
You need to actively monitor your system for weaknesses and address any issues promptly to stay compliant with MMAS standards. Common system weaknesses include residual inventory, system excess, and lost or found parts. By identifying and resolving these issues early, you can ensure that your material management and accounting system remains accurate and compliant with government regulations.
Audit trails and testing
To demonstrate the integrity and reliability of your system, auditors look for comprehensive audit trails and regular system testing. Maintaining a clear audit trail shows that your material management system is compliant and can withstand scrutiny. Regular testing ensures that your processes are accurate and meet the standards required by government contracts.
Physical inventories, receipts, returns, cycle/physical count materials
Accurate recordkeeping is essential for meeting the government’s compliance requirements. Regular physical inventories should be performed and reconciled with your book inventories. This also includes careful tracking of receipts, returns, and cycle or physical count materials to ensure your material management system is precise and compliant with MMAS standards.
Material transfers
When transferring materials, ensure you are accurately documenting and managing these transfers per the stipulated guidelines and controls outlined in the MMAS.
Material costing and borrow/payback
Consistent material costing and clear documentation of borrow/payback scenarios are essential to maintaining a compliant Material Management and Accounting System (MMAS). Proper tracking of these activities ensures that your material management records are accurate, and that they align with the standards required by government contracts. By adhering to MMAS guidelines, you’ll ensure your accounting system remains transparent and compliant with federal regulations, helping to avoid discrepancies during audits
Allocating common inventory
When managing common inventory, it’s essential to allocate materials accurately across multiple projects. This helps ensure that resources are distributed fairly and consistently within your material management processes. Proper allocation also prevents overuse or shortages, which could impact your compliance with MMAS requirements for government contracts. Clear documentation and accountability are key to maintaining transparency and meeting audit standards.
Commingled inventory
During an audit, disorder or confusion in your inventory management can raise red flags. To avoid this, it's critical to keep separate inventories clearly defined. Preventing the commingling of materials is a key compliance requirement under MMAS, as maintaining distinct records for different inventory categories helps ensure accuracy and transparency. Clear separation of inventory is essential to avoiding compliance issues and ensuring your material management practices meet the strict standards required by government contracts.
Regular reviews
Conducting regular, thorough internal audits is essential to validating your compliance with MMAS and addressing potential issues before they escalate. Proactively reviewing your processes helps you stay ahead of compliance challenges and avoid problems during external audits. To put it in sports terms: the best defense is a good offense.
By meeting these ten MMAS criteria, you ensure your operations remain efficient, reliable, and compliant. Integrating your enterprise resource planning (ERP) and inventory management solutions can streamline this process, making it easier to maintain compliance with government contracts and other regulatory requirements.
To learn more about MMAS requirements and how you can leverage them to benefit your business, download our new eBook, "How to Turn MMAS Compliance into a Competitive Advantage .” Discover how aligning with MMAS standards can give your organization a strategic edge in managing government contracts and ensuring operational efficiency.